Clasificación
Los fundamentos en los que se apoya esta propuesta de clasificación se dan en primera instancia, primera categoría del clasificación, e relación al a integridad del material original, básicamente debida bien sea al a perdida de mas, o bien debida a su conformación en modo de deformación. se presenta así, dos grandes grupos principales; uno por la conformación por desprendimiento de material (viruta), y un segundo gran grupo; por la conformación de toda la masa, forzada desde afuera con deformación mediante equipos.
en segundo termino , en una segunda categoría, en cuanto a la naturaleza de las fuerzas externas actuantes en el momento del a transformación del material base; esto es uno por maquinado; dos , de conformación mecánica de acción deformante de tipo plástico(no reversible), tres, la conformación forzada de polvos metálicos, cuatro, la conformación propiamente dicha por acción del calor sobre los estados fases del os materiales para acondicionarse a nuevas formas.
Materiales y manufactura
metales ferrosos:
los metales ferrosos como su nombre lo indica su principal componente es el fierro (hierro), sus principales características son su gran resistencia a la tensión y dureza. las principales aleaciones se logran con su estaño plata, platino, manganeso, vanadio y titanio.
su temperatura de fusión va desde los 1360ºc hasta los 1425ºc y uno de sus principales problemas es la corrosión
metales no ferrosos
por lo regular tienen menor resistencia a la tensión y dureza que los metales ferrosos, sin embargo su resistencia a la corrosión es superior
materiales no metálicos de origen orgánico:
son así considerados cuando contiene células animales o vegetales. estos materiales pueden usualmente disolverse en líquidos orgánicos con el alcohol o los tretracloruros, no se disuelven en el agua y no soportan altas temperaturas. unos de los representantes es el plástico.
materiales no metálicos de origen inorgánico.
son todos aquellos que no proceden de células animales o vegetales, o relacionados con el carbón. por lo regular se pueden disolver en agua y ne general resisten el calor menor que las sustancias orgánicas.
Sistemas de producción
Son sistemas que permitan lograr
eficientemente el tipo de producción que realiza, los sistemas de producción
consisten en mano de obra, equipos y procedimientos diseñados para combinar
materiales y procesos que constituyen sus operaciones de manufactura.Los
sistemas se dividen en 2 :
instalaciones: se refiere al equipo fisico,
apoyo de la manufactura: son los procesos usados por la compañía para
administrar la produccion y resolver problemas tecnicos y logisticos que
surgen en el ordenamiento de los materiales y el movimiento de los trabajos en
la planta, la seguridad de que los productos cumplan con las normas de calidad.
DIAGRAMA DE FASE
Diagrama Fe- C /tratamientos
térmicos
Diagrama de fase o diagrama de estados de la materia a la representación entre diferentes estados de la materia en función de variables elegidas para facilitar el estudio del mismo o cuando en una de estas representaciones todas las fases corresponden a estados de agregación diferentes se suele denominar diagrama de cambio de estado.
Clasificación de los aceros:
Los aceros se pueden clasficiar en función de varios criterios, esto da lugar a varias clasificaciones, la más utilizada de todas ellas es la clasificación en función del porcentaje de carbono disuelto:
El porcentaje de carbono disuelto en el acero condiciona las propiedades del mismo. Así cuanto mayor sea el porcentaje de carbono disuelto en el acero, éste presenta más dureza y más resistencia a la tracción. Teniendo esto presente es posible clasificar los aceros en:
Fundición con molde desechable (No permanente)
El molde donde se solidifica el metal debe ser destruido para mover la fundición. Estos moldes se hacen de arena, yeso o materiales similares que tienen su forma, usando aglomerantes de varias clases. La fundición en arena es el ejemplo más prominente. En la fundición de arena se vacía metal líquido dentro del molde hecho de arena. Después de que el metal se endurece, se sacrifica el molde a fin de recuperar la fundición.
Fundición con molde permanente
La fundición en molde permanente usa un molde metálico construido en dos secciones que están diseñadas para cerrar y abrir con precisión y facilidad. Los moldes se hacen comúnmente de acero o hierro fundido.
La cavidad junto con el sistema de vaciado se forma por maquinado en las dos mitades del molde a fin de lograr una alta precisión dimensional y un buen acabado superficial. Los metales que se funden comúnmente en molde permanente son: aluminio, magnesio, aleaciones de cobre y hierro fundido.
Pude usarse muchas veces para producir fundiciones en cantidad, es decir, tienen ciertas ventajas económicas en operaciones de alta producción. Está hecho de un metal o algunas veces de un refractario cerámico, que puede soportar las altas temperaturas de las operaciones de fundición. En este caso, el molde permanente consta de dos o más secciones que pueden abrirse para permitir la remoción de la parte terminada. La fundición en dados es el proceso más conocido de este grupo (Cuando se inyecta el metal fundido en la cavidad del molde a alta presión, las más comunes son de 7-350 MPa, la presión se mantiene durante la solidificación, posteriormente se abre el molde para remover la pieza).
La cavidad junto con el sistema de vaciado se forma por maquinado en las dos mitades del molde a fin de lograr una alta precisión dimensional y un buen acabado superficial. Los metales que se funden comúnmente en molde permanente son: aluminio, magnesio, aleaciones de cobre y hierro fundido.
Pude usarse muchas veces para producir fundiciones en cantidad, es decir, tienen ciertas ventajas económicas en operaciones de alta producción. Está hecho de un metal o algunas veces de un refractario cerámico, que puede soportar las altas temperaturas de las operaciones de fundición. En este caso, el molde permanente consta de dos o más secciones que pueden abrirse para permitir la remoción de la parte terminada. La fundición en dados es el proceso más conocido de este grupo (Cuando se inyecta el metal fundido en la cavidad del molde a alta presión, las más comunes son de 7-350 MPa, la presión se mantiene durante la solidificación, posteriormente se abre el molde para remover la pieza).
CERÁMICOS:
es un tipo de material inorgánicos que es
un buen aislante y tiene una temperatura de fusión y resistencia muy elevada.
estos materiales por sus propiedades son imposibles de fundir y de mecanizar
por unos medios diferentes y para ello se realiza un procesos de
caracterización.
TRABAJOS EN VIDRIO
El vidrio se fabrica a partir de una mezcla compleja de compuestos vitrifican tes como sílice fundentes como los álcalis y estabilizan tes como la cal estas materias primas se cargan en el horno de cubeta de producción continua por medio de una tolva el horno se calienta con quemadores de gas o petróleo
VIDRIO
es un material cerámico que se fabrica a
partir de unos materiales inorgánicos a una temperatura extremadamente alta en
el cual su fabricación consta de unos procedimientos los cuales son:
-preparación de la materias primas
-fusión
-formado del vidrio
-recocido
-acabado
PROCESAMIENTOS DE POLVOS,CERÁMICOS Y
METÁLICOS:
-polvo: Todos los metales pueden producirse
en forma de polvo, sin embargo no todos cumplen con las características
necesarias para poder conformar una pieza. Los dos metales más utilizados para
la producción de polvo para la fabricación de piezas son el cobre y el hierro.
Como variaciones del cobre se utilizan el bronce para los cojinetes porosos y
el latón para pequeñas piezas de máquinas. También se llegan a utilizar otros
polvos de níquel, plata, tungsteno y aluminio.
-cerámicos: La mayoría de los
productos cerámicos tradicionales y técnicos son manufacturados compactando
polvos o partículas en materiales que se calientan posterior mente a enormes
temperaturas para enlazar las partículas entre si. Las etapas básicas para el
procesado de cerámicos por aglomeración de partículas son:
1. preparación del material.
2. moldeado o colada;
3. tratamiento térmico del secado y
orneado por calentamiento de la pieza de cerámica a temperaturas
suficientemente altas para mantener las partículas enlazadas.
-metálicos: Se denomina fundición y también
esmelter al proceso de fabricación de piezas, comúnmente metálicas pero también
de plástico, consistente en fundir un material e introducirlo en una cavidad,
llamada molde, donde se solidifica.
El proceso mas tradicional es la fundición
en arena, por ser ésta un material refractario muy abundante en la naturaleza y
que, mezclada con arcilla, adquiere cohesión y moldeabilidad sin perder la
permeabilidad que posibilita evacuar los gases del molde al tiempo que se
vierte el metal fundido.
PROCESOS EN CONFORMADOS EN POLÍMEROS:
Son macromoléculas formadas por unidades
más pequeñas que se repiten llamado monómeros y se clasifican de la siguiente
manera:
· Polímeros Naturales: son aquellos
provenientes directamente del reino animal o vegetal como el algodón, seda,
lana, celulosa, almidón, proteínas, caucho natural (látex o hule), ácido
nucleicos como el ADN entre otros.
· Polímeros Semisinteticos: son aquellos
que se obtienen de la transformación de polímeros naturales por ejemplo
nitrocelulosa o el caucho vulcanizado.
· Polímeros sintéticos: son los
transformados o creados por el hombre, entre ellos están los plásticos, los más
comunes en la vida cotidiana son el polietileno, el pvc, poliestireno; la gran
variedad de las propiedades físicas y químicas de estos elementos permite
aplicarlos en la construcción, embalaje, industria automotriz, aeronáutica,
electrónica, agricultura y medicina.
EXTRUSIÓN: la extrusión consiste en hacer
pasar bajo la acción de la presión un material termoplástico a través de un
orificio con formas más o menos complejas (hilera), de manera tal y continua,
que el material adquiera una sección transversal igual a del orificio. En la
extrusión de termoplásticos el proceso no es tan simple, ya que durante el
mismo, el polímero se funde dentro de un cilindro y posteriormente, enfriado en
una calandria. este proceso tiene por objetivos, proceso que es normalmente continuo,
usarse para la producción de perfiles, tubos, películas plásticas, hojas
plásticas, etc.
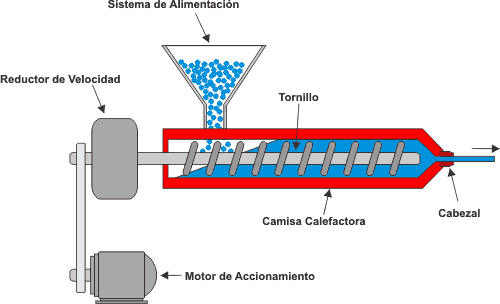
La extrusora de plástico es la máquina que
se utiliza para el proceso de extrusión de polímeros. Ésta toma la forma del
material fundido y lo hace fluir por medio de un orificio de un dado para
producir un producto largo y continuo cuya forma de la sección
transversal queda determinada por la forma de la boquilla. En el vídeo anterior
el polímero sale en forma de hilos largos y extensos.
TERMO FORMADO: Se refiere al proceso en
el que una lámina de cualquier polímero termo plástico es calentada hasta llegar
a su temperatura de transición vítrea quedando apta para su deformación.
Seguidamente esta lámina plástica se coloca sobre el molde con la forma deseada
y se succiona con vacío contra éste, para que copie exactamente su forma,
obteniendo la pieza plástica.

La fabricación de un molde para
exhibir ropa en supermercados es realizado por medio del termoconformado como
se observa en el vídeo. Primeramente se calienta la lamina del plástico para
después pueda tomar la forma del molde.El termoconformado tiene muchas
aplicaciones sobre todo en aquellos casos donde es necesario la aplicación de
un molde para la fabricación.
INYECCIÓN: Es un proceso físico y
reversible, en el que se funde una materia prima llamada termoplástico, por el
efecto del calor, en una maquina llamada inyectora. Esta máquina con el
termoplástico en estado fundido, lo inyecta, dentro de las cavidades huecas de
un molde. Con una determinada presión, velocidad y temperatura. Transcurrido un
cierto tiempo, el plástico fundido en el molde, va perdiendo su calor y
volviéndose sólido, copiando las formas de las partes huecas del molde donde ha
estado alojado. El resultado es un trozo de plástico solido pero con formas
dimensionales similares a las partes huecas del molde. A este termoplástico
solidificado le llamamos inyectada.
Los Pellets son introducidos en la
inyectora como materia prima para que luego sean fundidas por medio del calor y
poder ser inyectadas a presión en un molde. Cuando el molde está terminado, el
objeto es liberado y enfriado para completar su fabricación.
INYECCIÓN SOPLADO: Es el tercer método más
utilizado en el procesado de plásticos. Durante mucho tiempo se empleó casi
exclusivamente para la producción de botellas y botes, sin embargo los últimos
desarrollos en el proceso permiten la producción de piezas de geometría
relativamente complejas e irregular, espeso de pared variable, dobles capas,
materiales con altas resistencias químicas, etc.
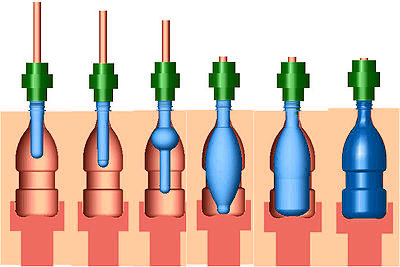
Básicamente el proceso de soplado está
pensado para su uso en la fabricación de productos de plásticos huecos. Aunque
hay diferencias considerables en los diferentes procesos de soplado, todos
tienen en común la producción de un precursor o preforma, su colocación en un
molde hembra cerrado, y la acción de soplarle con aire para expandir el
plástico fundido contra la superficie del molde, creando así el producto final.
MATERIALES COMPUESTOS:
Se entiende por materiales compuestos
aquellos formados por dos o más materiales distintos sin que se
produzca reacción química entre ellos.
En todo material compuesto se distinguen
dos componentes:
- la MATRIZ, componente que se presenta en
fase continua, actuando como ligante
- el REFUERZO, en fase discontinua, que es
el elemento resistente.
PROCESAMIENTO DE CERMET:
Un cerment es un ladrillo de cermaica
formado por materiales ceramicos y metales. su nombre viene del nombre ceramic
metal, los cerments estan diseñados para combinar la resistencia a
altas temperaturas y a la abrasión de los ceramicos con la maleavilidad de los
metales. como matriz se usa el metal, usual mente niquel, molibdeno o cobalto,
y la fase dispersa esta constituida por carburos, refractarios,oxidos,boruros.
FORMADO DE METAL:
DEFORMACION PLASTICA:
Debido a que los metales deben ser
conformados en la zona de comportamiento
plástico es necesario superar el límite de
fluencia para que la deformación sea
permanente. Por lo cual, el material es
sometido a esfuerzos superiores a sus límites
elásticos, estos límites se elevan
consumiendo así la ductilidad.
DOBLADO:
El doblado de metales es la deformación de
láminas alrededor de un determinado
ángulo. Los ángulos pueden ser clasificados
como abiertos (si son mayores a 90
grados), cerrados (menores a 90°) o rectos.
Durante la operación, las fibras externas
del material están en tensión, mientras que
las interiores están en compresión. El
doblado no produce cambios significativos
en el espesor de la lámina metálica.
Existen diferentes formas de doblado, las más
comunes son: doblado entre dos
formas y doblado deslizante.
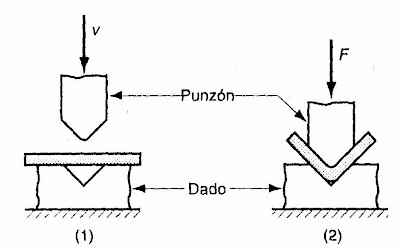
Doblado entre formas:
En este tipo de doblado, la lámina metálica
es deformada entre un punzón en forma
de V u otra forma y un dado. Se pueden
doblar con este punzón desde ángulos muy
obtusos hasta ángulos muy agudos. Esta
operación se utiliza generalmente para
operaciones de bajo volumen de producción.
Doblado Deslizante:
En el doblado deslizante, una placa
presiona la lámina metálica a la matriz o dado
mientras el punzón le ejerce una fuerza que
la dobla alrededor del borde del dado.
Este tipo de doblado está limitado para
ángulos de 90°.
EMBUTIDO:
El embutido consiste en colocar la lámina
de metal sobre un dado y luego
presionándolo hacia la cavidad con ayuda de
un punzón que tiene la forma en la cual
quedará formada la lámina.
Un ejemplo de embutido es la fabricación de
una copa metálica. Para este caso, un
blanco de diámetro Db es embutido en un
dado por un punzón de diámetro Dp. Los
radios en las esquinas del dado y el punzón
están dados por Rp y Rd. El punzón
ejerce una fuerza F hacia abajo para lograr
la deformación del metal; además, una
fuerza Fh es aplicada hacia abajo por la
placa sujetadora, que estabilizará el flujo de
la lámina para que éste sea parejo. El
punzón baja hasta que la lámina ha quedado
introducida en la luz entre punzón y
matriz, y el resultado es una pieza fabricada en
forma de cilindro de diámetro Dp
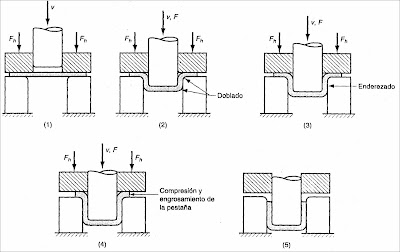


LAMINADO:
es un proceso en el que se reduce el
espesor de una pieza larga a
través de fuerzas de compresión ejercidas
por un juego de rodillos, que giran
apretando y halando la pieza entre ellos.
El resultado del laminado puede ser la
pieza terminada (por ejemplo, el papel
aluminio utilizado para la envoltura de
alimentos y cigarrillos), y en otras, es la
materia prima de procesos posteriores, como
el troquelado, el doblado y la
embutición.
Generalmente el laminado se realiza en
caliente como se ilustra en la Figura No. 15.
Este proceso comienza con una colada
continua en donde se recalienta el acero en
un foso de termodifusión, luego el acero
pasa por una serie de rodillos que
desbastan el material (proceso laminado) y
finalmente la lámina es almacenada en
rollos.
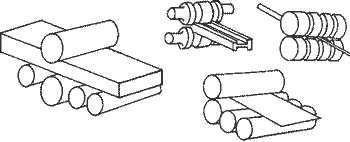
FORJADO:
El forjado fue el primero de los procesos
del tipo de compresión indirecta y es
probablemente el método más antiguo de
formado de metales. Involucra la aplicación
de esfuerzos de compresión que exceden la
resistencia de fluencia del metal.
En este proceso de formado se comprime el
material entre dos dados, para que tome
la forma deseada. Existen tres tipos de
operación de forjado.
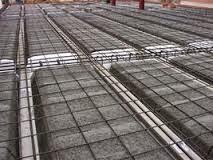.jpg)
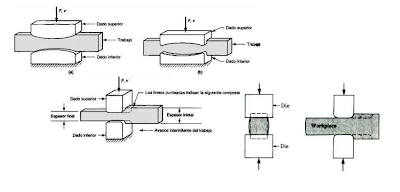
EXTRUCCIÓN
La extrusión es un proceso por compresión
en el cual el metal de trabajo es forzado
a fluir a través de la abertura de un dado
para darle forma a su sección transversal.
Ejemplos de este proceso son secciones
huecas, como tubos, y una variedad de
formas en la sección transversal.
Los tipos de extrusión dependen básicamente
de la geometría y del material a
procesar. Existe el proceso de extrusión
directa, extrusión indirecta, y para ambos
casos la extrusión en caliente para metales
(a alta temperatura).
En la extrusión directa, se deposita en un
recipiente un lingote en bruto llamado
tocho, que será comprimido por un pistón,
Al ser comprimido, el material se forzará a fluir por el otro extremo adoptando
la forma que tenga la geometría del dado.

CORTE:
Este proceso queda de alguna manera
fuera de lugar en nuestra lista de procesos de
deformación, debido a que implica más el
corte que el formado del metal. En esta operación se corta
la parte usando un punzón y un dado, como
se muestra en la figura 3.2 (c). Aunque éste no es un
proceso de formado se incluye aquí debido a
que es una operación necesaria y muy común en el
trabajo de láminas metálicas.

TREFILADO:
Los rodillos giran para jalar el
material de trabajo y simultáneamente apretarlo entre ellos. el proceso de
laminado plano se usa para reducir el espesor de una sección transversal
rectangular.


PROCESOS DE FUNDICIÓN:
TIPOS DE SOLDADURA:
Se pueden distinguir primeramente los
siguientes tipos de soldadura:
- Soldadura heterogénea. Se efectúa entre
materiales de distinta naturaleza, con o sin
metal de aportación: o entre metales
iguales, pero con distinto metal de aportación. Puede ser
blanda o fuerte.
- Soldadura homogénea. Los materiales que
se sueldan y el metal de aportación, si lo
hay, son de la misma naturaleza. Puede ser
oxiacetilénica, eléctrica (por arco voltaico o por
resistencia), etc. Si no hay metal de
aportación, las soldaduras homogéneas se denominan
autógenas.
Por soldadura autógena se entiende aquélla
que se realiza sin metal de aportación, de
manera que se unen cuerpos de igual
naturaleza por medio de la fusión de los mismos; así, al
enfriarse, forman un todo único.
SOLDADURA BLANDA:
Esta soldadura de tipo heterogéneo se
realiza a temperaturas por debajo de los 400 oC.
El material metálico de aportación más
empleado es una aleación de estaño y plomo, que
funde a 230 oC aproximadamente.
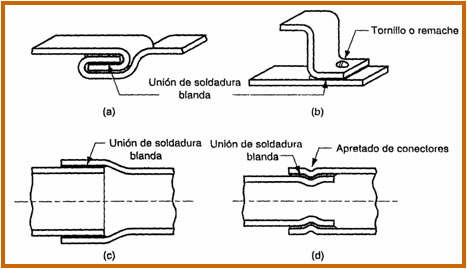
SOLDADURA FUERTE:
También se llama dura o amarilla. Es
similar a la blanda, pero se alcanzan
temperaturas de hasta 800 oC. Como metal de
aportación se suelen usar aleaciones de plata, y
estaño (conocida como soldadura de plata);
o de cobre y cinc . Como material fundente para
cubrir las superficies, desoxidándolas, se
emplea el
bórax. Un soplete de gas aporta el calor
necesario para la
unión. La soldadura se efectúa generalmente
a tope, pero
también se suelda a solape y en ángulo.
Este tipo de soldadura se lleva a cabo
cuando se
exige una resistencia considerable en la
unión de dos
piezas metálicas, o bien se trata de
obtener uniones que
hayan de resistir esfuerzos muy elevados o
temperaturas
excesivas. Se admite que, por lo general,
una soldadura
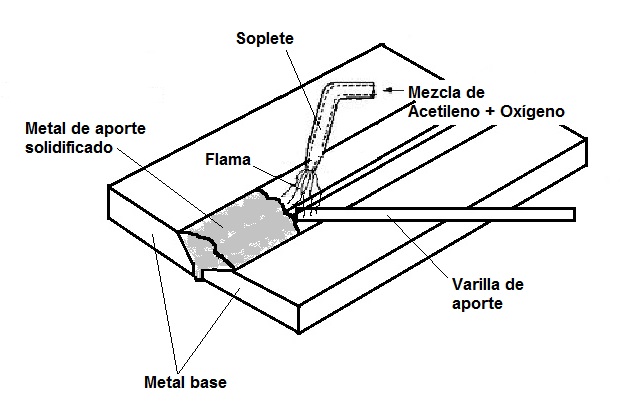
fuerte es más resistente que el mismo metal
que une.
No hay comentarios:
Publicar un comentario